
Wilfley’s WCD4 Material & Static Seal Greatly Reduces Parts Wear and Seal Leaking Issue at Ethanol Plant
Country:
USA
Market:
Ethanol
Product :
A9 pump, WCD4 material.
Background
Over 90 percent of the grain ethanol produced today comes from the dry milling process, with the remaining coming from wet mills. The main difference between the two is in the initial treatment of the grain. In dry milling, the entire grain kernel is first ground into “meal”, then slurried with water to form a “mash”. Enzymes are added to the mash to convert starch to sugar. The mash is cooked, then cooled and transferred to fermenters. Yeast is added and the conversion of sugar to alcohol begins. After fermentation, the resulting “beer” is separated from the remaining “stillage”. The ethanol is then distilled and dehydrated, then blended with about 2% denaturant (such as gasoline) to render it undrinkable. The stillage is sent through a centrifuge that separates the solids from the solubles. These co-products eventually become distiller’ grains, as well as corn distiller oil.
The Challenge
One of the main challenges is pumping the beer mash during the process which is very abrasive. A plant in Nebraska was experiencing significant wear to the wet-end components of their Beer Bottoms pump. The wear required the pump to be completely rebuilt or replaced at every 6 -month shutdown. The customer was also experiencing constant mechanical seal leakages which occurred after a few weeks of operation. The customer would allow the seal to leak until the scheduled 6-month shutdown at which time they would also replace the seal.
The Solution
Due to Wilfley’s experience pumping ethanol, the customer reached out to their Wilfley Rep to see if there were any options to address the material wear and seal failures. After thoroughly reviewing the application, it was decided that a Wilfley A9 6×4 pump in Wilfley’s WCD4 material and utilizing our dynamic seal with a SolidLock static seal was the proper pump combination for the application. Wilfley’s WCD4 provides a 38% increase in hardness over standard CD4. (WCD4 = 345 HBN Standard CD4 = 255 HBN)
The Result
The competitor’s pump was removed from the service and the Wilfley A9 pump with WCD4 wetted materials and the combination dynamic seal & SolidLock static seal was installed. The pump ran for little over a year without any issues and to the customer’s satisfaction. So, during a scheduled shutdown, the customer opened the pump just to check the wetted parts for wear. There was so little wear, the customer re-assembled the pump and put it back in service for another year. The pump has been in service almost 5 years with virtually no maintenance required. The customer has since purchased a second Wilfley A9 pump.
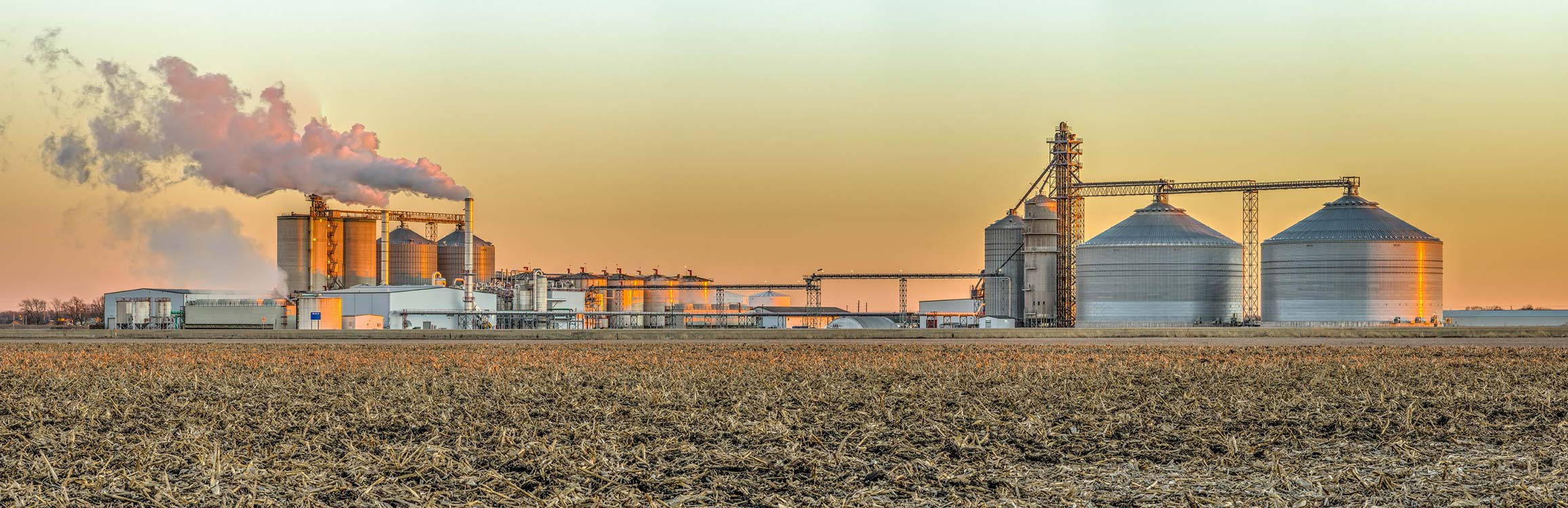
Annual Savings Utilizing the Wilfley Pump in WCD4 with SolidLock Seal
Annual Parts Savings | Annual Seal Savings | Annual Labor Savings | Total Annual Savings |
$15,000 | $3,600 | $780 | $19,380 |
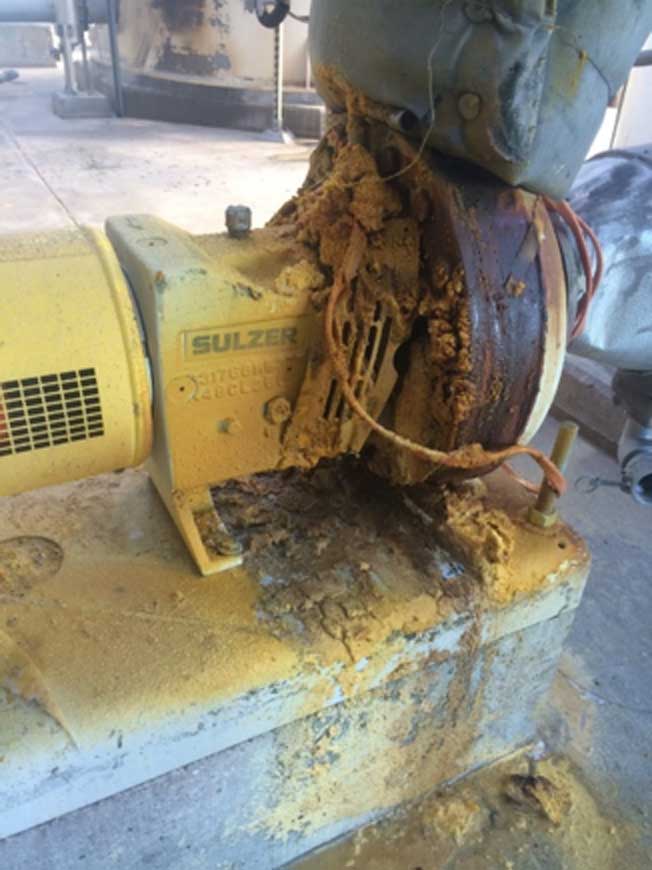
Competitor Pump
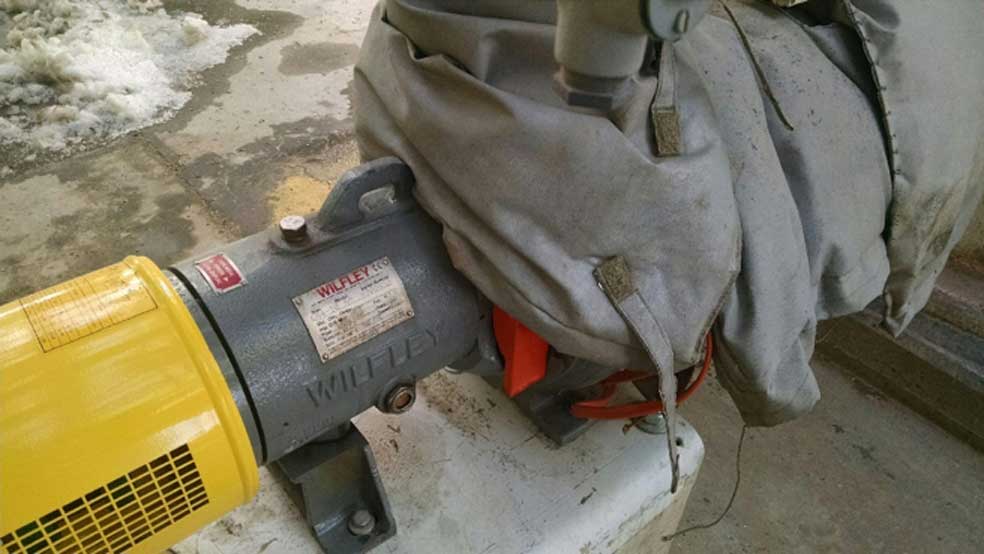
Wilfley Pump
Wilfley’s WCD4™ duplex stainless steel is ideal for erosion‑corrosion applications in extremely corrosive environments
WCD4™ is a specially processed duplex stainless steel that is chemically similar to ASTM A890 (cast material) or UNS S32550 (wrought material) but with significantly improved mechanical properties and corrosion resistance.
WCD4™ is ideal for erosion-corrosion applications in extremely corrosive environments. Pump wear parts made from WCD4™ are expected to have exceptional wear life due to its increased hardness and improved corrosion resistance.
Mechanical Properties
Material | Average Hardness | Minimum Tensile Strenght | Minimum Yield Strenght | Minimum Elongation |
Wilfley WCD4 | 345 HBN | 164,000 psi (1,131 MPa) | 113,000 psi (779 MPa) | 16% |
Standard CD4 | 240 HBN | 100,000 psi (699 MPa) | 70,000 psi (483 MPa) | 16% |
Improvement | 38% | 64% | 61% | Same |
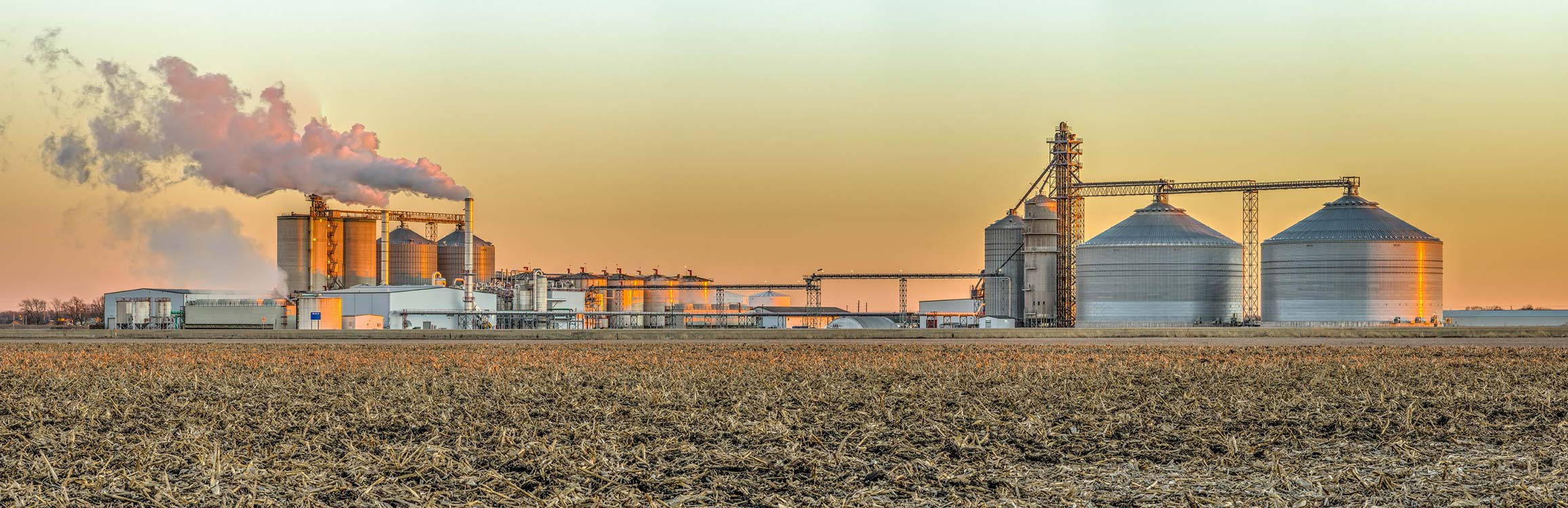